In more than a decade of working with water utilities around the globe on Central Event Management (CEM) system implementations, I’ve repeatedly seen that the network management challenges that managers think they’re facing are (almost literally) only the tip of the iceberg. The issues that lie underneath are far less obvious, or even invisible, becoming apparent only after the CEM system has been working for some time.
7 layers of challenges – from visible to obscured

Water network management challenges manifest in seven layers. The top two, being non-revenue water (NRW) challenges, are highly visible. It is the first of these – physical water losses, and often the associated energy wastage – that typically prompts most utilities to embark on a Central Event Management project. But later, the process of implementing and working with the CEM often reveals other challenges. In some cases, our customers have found hidden issues that may have existed for a long time but became visible only after beginning to use the CEM system. At other utilities, managers were aware of an additional challenge, but they didn’t realize the extent of it or how to address it.
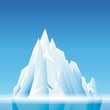
The most-recognized challenges
Minimizing non-revenue water is at the top of most water utilities’ priorities, and it’s often first on the agenda when we speak with utilities about their network challenges.
Layer 1 – Physical water losses:
Sometimes called real losses, physical water losses are made up of leakage from transmission and distribution mains, leakage and overflows at storage tanks, and leakage on service connections up to the point of the individual customer meter. As the most visible challenge, the value of centralized water management for reducing physical water loss is likewise easy to see.
Early detection, quantification of water loss and identification of hidden and slow-developing leaks can significantly reduce physical water loss, potentially saving millions of dollars, especially if energy wastage is included.
Layer 2 – Apparent water losses:
Unauthorized consumption and inaccurate customer meters, including at large industrial customers, are common and costly. However, the visibility in meter degradation at large consumers’ sites and the automatic water balance calculations provided by a CEM system can yield savings fairly quickly.
For example, a large Australian water utility was suffering from significant NRW losses. With the very first alert generated by the CEM system, it discovered a leaking pipe that it then acknowledged might have been leaking for more than two years. As it continued working with the system, the utility began to look at proactive ways to identify areas with high unmetered consumption, identifying points of apparent water loss that it was then able to rectify. They told us that the CEM system prevented about 6.5 billion liters of water loss based on an annualized calculation.
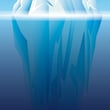
5 Less-visible layers of challenges
Layer 3 – Data quality:
Having invested in sensors across their network, many utilities assume that they’re getting all the data that they should. But problems in the collection and transmission of data are not uncommon, whether caused during deployment or by faults that develop over time. Such problems often go unnoticed until a CEM system is up and running. One customer said they were surprised to discover that 30% of sensors in their network were not working correctly, even though the sensors were relatively new. It was the first they knew of a gap in their data. Another data-related problem that afflicts many utilities is the “data tsunami”. They struggle to cope with all the data generated across the network, and as time goes on and their network grows, they can’t scale up to handle even larger volumes of data. By providing a single platform that analyzes data from large numbers and multiple types of sensors, a CEM system turns a flood of incomprehensible data into meaningful, easily understood information.
Layer 4 – Operational efficiency:
Many utilities struggle to manage and prioritize allocation of resources. Until they are well into deployment of the CEM, they often cannot see where their greatest costs lie. A CEM system can make it easy to make informed decisions about where best to direct limited resources to achieve the greatest savings. For example, at a South American utility that had a high rate of false alarms from sensors and was struggling with analyzing meter data, readings that indicated unresolved problems were being ignored. As a result, detection efforts were very inefficient – every 100 leak detection jobs would yield 40 dry holes. However, once the utility had a single view of all relevant information via its CEM system, which also defined the DMA-based geographic boundary of each leak and provided a platform for easy communication across departments, the dry hole rate dropped by 50%.
Layer 5 – Customer satisfaction and quality of service:
Many utilities tell us they struggle with low customer satisfaction and poor service quality. They want to improve their customers’ experience and better comply with regulations, but the underlying issues are difficult to see. Over time, as a CEM system “learns” their network, they gain pinpoint visibility into hidden and slow-developing leaks, water quality events, and water pressure events. As a result, they can respond quicker and more effectively, leading to shorter repair cycles, less service downtime and more consistent water pressure, often solving issues before they are noticed by consumers. The experience of a regional utility in Spain, which halved the repair time for invisible leaks that otherwise would have gone undetected, is not uncommon.
Layer 6 – Data and knowledge retention:
Recruiting new expert employees to replace their aging workforce is a challenge for man utilities around the globe. And even when you can find skilled employees, how do you replace the in-depth network knowledge that key employees have accumulated over decades? Utilities whose legacy team is still largely intact might not have thought much about this, but it’s a challenge that will come soon for many of them.
We’re already worked with several utilities that discovered that with the automatic detection of events, user-friendly, single dashboard to manage multi-source information, and historical log of events and activities provided by their CEM system, they are able to cover shortfalls in employee skills and knowledge.
Layer 7 – Planning challenges:
Limited ability to proactively plan maintenance of assets is an ongoing issue that lies behind many of the challenges already mentioned. By providing insight into multiple aspects of network performance, a CEM system enables utilities to make strategic decisions around prioritizing investments and scheduling maintenance, enabling them to proactively prevent many problems and reducing the need for reactive actions.